Concrete Batch Plants
Stationary Type Concrete Batch Plants
Production capacity of our Stationary Type Concrete Batching Plants are classified as 30, 60, 100, 120, 160, 200 and 240 m3/h. As per customer needs and capacity requirements, two sets of mixers can be used at the same time in one concrete plant. We may design what you need, we have got unlimited design capability. Twin Shaft Mixers, Single Shaft Mixers, Planetary Mixers and Pan Mixers are the mixer types that are used in our Stationary Type Concrete Mixing Plants according to the desired concrete type to be produced. Our Stationary Concrete Batching Plants are equipped with high technology control systems that include premium quality and made in Europe, SIEMENS and SCHNEIDER brands electronic components and PLC module. All units of the plant are controlled through an advanced software which has sophisticated features and user friendly interface. For urgent cases, manual control panel is also present.
Our Stationary Type Concrete Mixing Plants are equipped with different sizes of cement silos according to production capacity and application purposes. From 30 to 5.000 tons capacity cement silos can be used in our Stationary Concrete Plants. Cement silos up to 50 tons capacity are manufactured as bolted and welded type. Silos having capacity above 50 tons are preferred as bolted type for easy transport. Our cement silos are equipped with air filter against dust, pressure relief (safety) valve, level indicators, butterfly valves and air nozzles. Our company knows very well that the climate conditions have major effects on the quality of concrete. While Stationary Concrete batching plants in cold-climate regions such as Russia, Kazakhstan, Ukraine, Northern Europe etc. are being heated by hot vapor generators and insulated panels, the concrete water to be used in concrete plants in hot-regions such as Middle East, GCC or Africa countries is cooled by chillers. Aggregate pre-feeding systems are our alternative solutions to the loading ramps which are necessary for charging the hoppers by loaders. In case of using aggregate pre-feeding systems, requirement of loading ramp is removed. Different layouts and site plans for Stationary Concrete Plants are applied according to the conditions of the area where the concrete plant is to be installed.
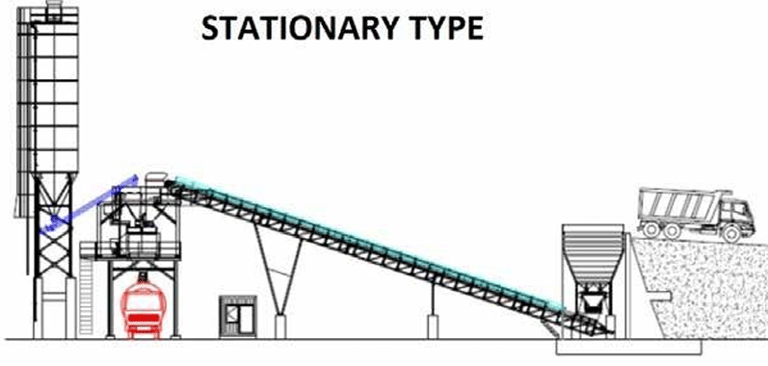
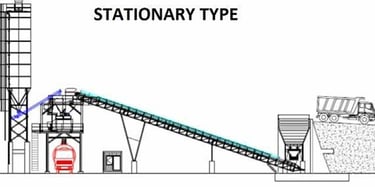
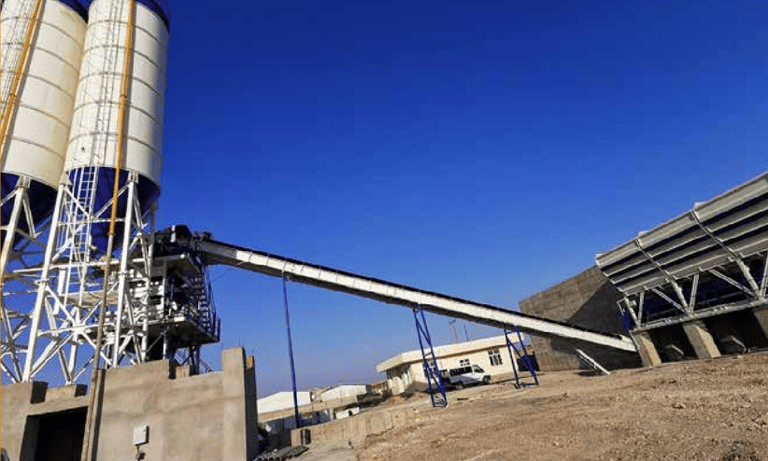

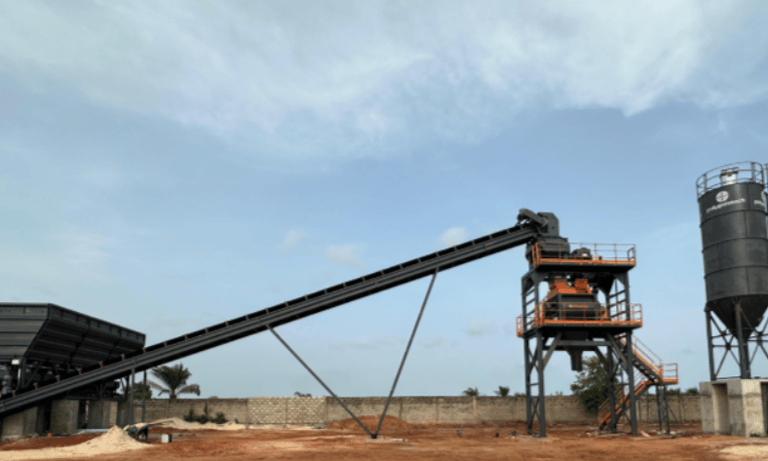

Mobile Type Concrete Batch Plants
Mobile Plants consist of Mobile Concrete mixers are designed to be mobile and by this way are installed on towable chassis with wheels for maximum mobility and quick setup. Mobile Batching Plants are best solution for temporary construction sites or construction projects where the equipment would only be needed for specific and limited appliance area of the projects. Mobile Concrete Plants can be easily installed and disassembled and additionally necessitate very minimal preparation or set up before using it. Being used at almost all construction projects, concrete is now produced at concrete plants with delicate scaling and high mixing possibility. Aggregate, cement, water and additives are scaled with high precision at weighing scales as per the concrete recipes assessed as per previous laboratory tests and are mixed homogeneously by high efficiency fast concrete mixers to produce high quality concrete.
Before the Mobile Concrete Plants, construction companies were providing concrete from ready-mixed concrete companies if there is any near the project area, or they were establishing a Stationary Concrete Plant for their project. However, in some countries and for some projects, this procurement way increased the costs of the construction companies as well as caused them not to supply high-quality concrete on time. Various types of Mobile Concrete Plants offer appropriate solutions for any projects, allowing all construction companies to be more independent and more flexible regarding the concrete production for their projects. An aggregate hopper where the aggregate is stored, an aggregate weighing conveyor on which the aggregate is weighed, a cement-weighing scale, a water-weighing scale, a chemical-weighing scale and a concrete mixer for mixing all these materials homogeneously and quickly are placed on the main unit. Axles and wheels are placed on the back of the main unit. The truck tractor can be attached to the king pin located at the front of the main unit and can transport the main unit. The European motorways standards are also taken into consideration to determine external dimensions when designing the Mobile Concrete Plant; thus, the unit is suitable for transportation to distant countries by road with a special permit. The mobile plant can be easily shipped to any countries by means of maritime transport. The main unit is shipped as an open load but other units are easily placed inside the container. Other units required for the Mobile Concrete Plant, i.e. cement silo, cement conveyor, cement silo filter and aggregate pre-feeding system, can be transported with standard trucks or containers. In Mobile Concrete Plants, aggregate hoppers are generally square type hoppers where two aggregate chambers are placed on one side and the other two aggregate chambers on the opposite side.
A Mobile Concrete Plant consists of the same units as in a Stationary Concrete Plant, where these units are fixed on a chassis with axles and wheels. When this chassis is towed by a tractor, the Mobile Concrete Plant can easily be transported to other locations. Due to its robust structure, Mobile Concrete Plant with 2 complete sets of screw conveyors, filters and other silo equipment can be transported with the help of only one single trailer truck. When compared to Stationary Concrete Plant, Mobile Concrete Plant offer the following advantages to its users: 1. Easier to transport. The main unit of a Mobile Concrete Plant can be transported by a truck tractor. 2. Faster and easier installation, disassembling and translocating. Flexibility. 3. Less installation space. Installable within the project area. 4. Less concrete foundation requirement. Installable on a flat concrete floor. 5. Easier installation permission. In some cases, no permission is required. The above mentioned advantages allow project-based construction companies to have great flexibility and to make significant savings in their total costs. Mobile Concrete Plants are mostly preferred by construction companies for their project-based works. Mobile Concrete Plants are the product of a sophisticated engineering work. All units are placed in a smaller area through aesthetic design. They are also preferred by ready mixed concrete companies for major construction projects to which they supply concrete, by establishing a Mobile Concrete Plant within the area of a project to make concrete production only for that project.
Aggregate hopper can be filled through a concrete/steel aggregate loading ramp or more effectively through Aggregate Pre-Feeding System. There are two types of Aggregate Pre-Feeding System.
1- Compact Aggregate Pre-Feeding System ( Can be shipped via a Truck or Container )
2- Mobile Aggregate Pre-Feeding System ( Just like the Mobil main unit, axles and wheels are placed at the back and it can be transported by a truck tractor )
In high capacity Mobile Concrete Plants, four chamber linear type ( in-line type ) aggregate hoppers are used. Mobile Plant Equipment necessary for the operation of the batch plant is installed on the main chassis and is being transported on it. The electricity cabling and water and pneumatic system piping on Mobile Concrete Plants are generally installed during the production of the plant at the factory. This allows to save considerable time at the place of installation and shortens the installation time of the Mobile Plant. A Stationary Concrete Plant with medium capacity can be installed in 14-21 days, whereas the Mobile Concrete Plant can be installed in 7-9 days. A thin and flat concrete basement is usually enough for Mobile Concrete Plants. There is no need for concrete foundations with a certain height as required for Stationary Concrete Plants. This provides the user with a significant advantage in terms of concrete foundation costs that should be borne for each installation. Mobile Concrete Plants are equipped with weighing conveyors and weighing hoppers of high weighing precision. All concrete production process is carried out with a fully automatic and computerized PLC control system. With a SCADA based concrete production software, concrete can be produced in accordance with the concrete recipe, and all parameters can be controlled and recorded. The concrete mixer with high weighing precision and high technology directly affects the quality of concrete.
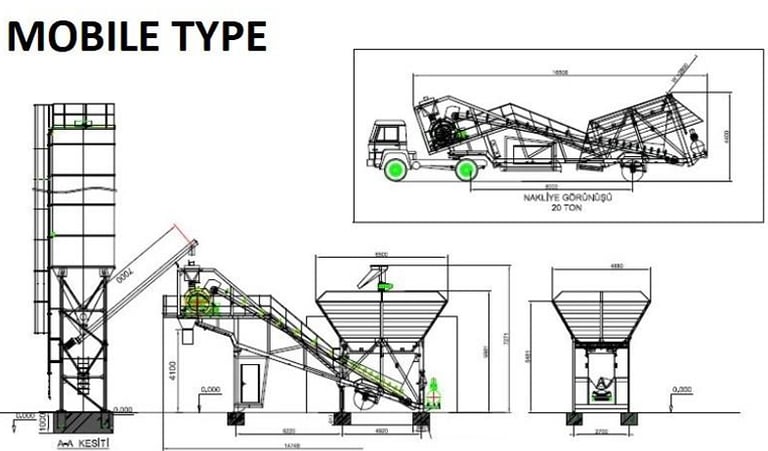
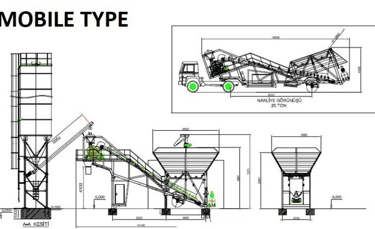
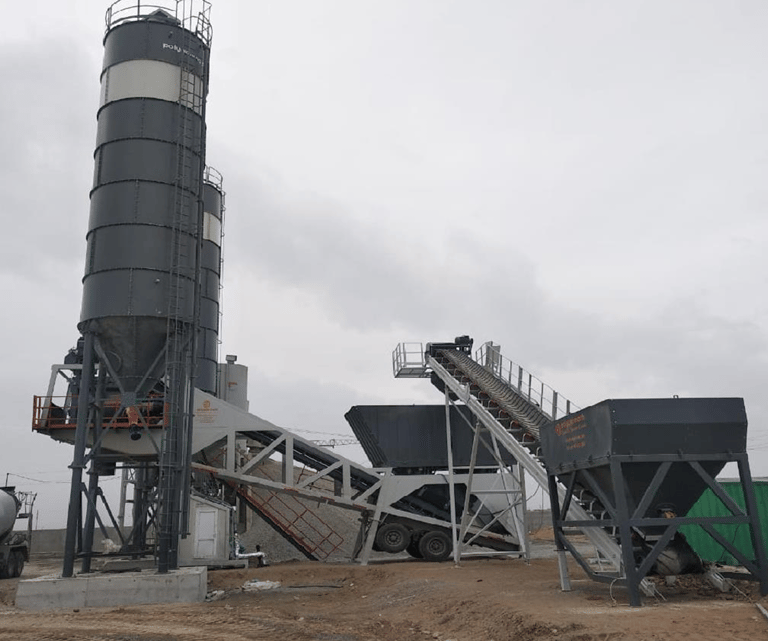
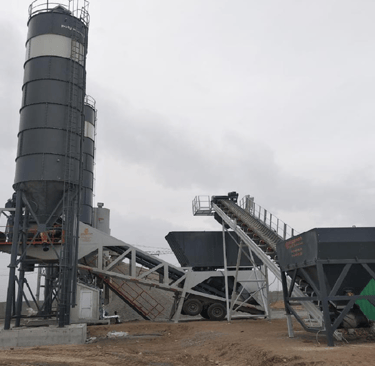


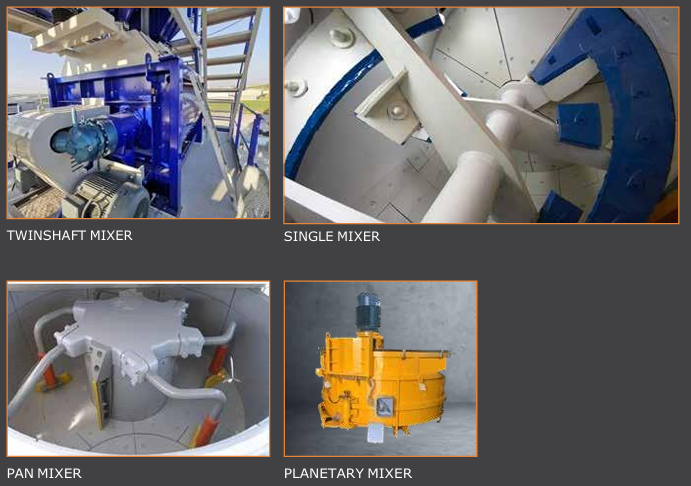
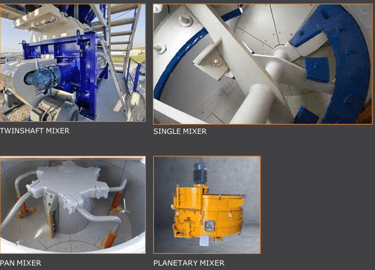
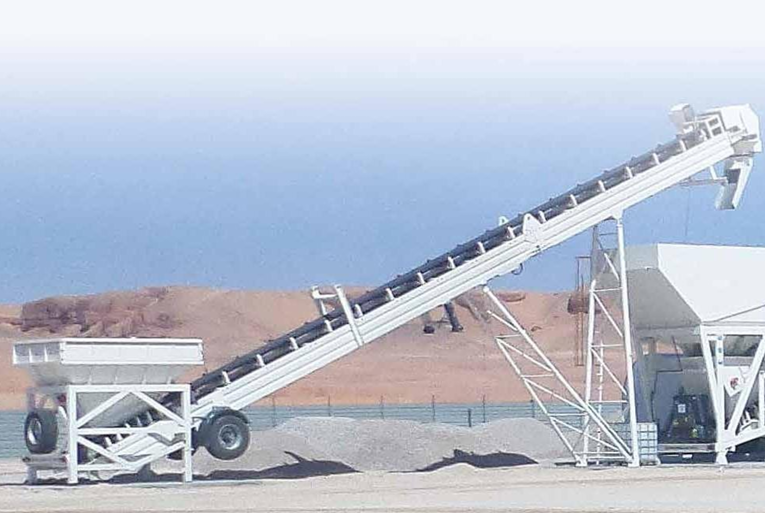
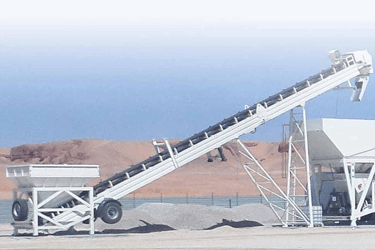