Crushing and Screening Plants
STATIONARY CRUSHING AND SCREENING PLANTS:
Crushing and Screening Equipment is designed and manufactured with different configurations and capacity values according to customer needs and preferences. The production capacity value of our crushing and screening equipment varies from 50 to 1.000 tph. The configuration and layout of our crushing and screening equipment are defined according to different standards, such as
• Required production capacity
• The type, hardness and abrasiveness grade of the material to be crushed,
• Maximum size of feed
• The size of the final score required.
Working Principle of Crushing and Screening Plants
A stationary crushing plant in a mining operation or quarry site is one that is permanently installed as opposed to one that has been mounted on a wheeled frame or perhaps on skids. It is a configuration fitted with several crushers, screens, conveyors, and feeding devices. The stationary crushing plants are capable of highly efficient and effective crushing and screening in their appropriate design and arrangement. Conversely, static crushing plants are fixed in one location in contrast with portable or mobile crushing plants.
Their long lifespan makes the plants very well-suited for large mining, quarrying, and recycling applications where the volume and consistency of the material being processed call for a reliable long-term solution with high productivity. Portable crushing plants can be custom-designed to operate exactly according to specific operational requirements. Certain factors include type of material to be processed, capacity requirements, end-product specifications, and spatial constraints unique to the site. This degree of personalization will offer a customized solution that maximizes the profitability and productivity of operations, considering enabling the plant to manage the expected throughput and material properties. Operations also integrate modern technology features such as automation and monitoring systems, which afford operators precise control over the crushing process, further improving their efficiency, safety, and scalability. The stationary crushing plant, as the name suggests, is constructed robustly and optimized to suit large-scale production of high-quality materials that are needed in infrastructure construction and other important sectors. Thus, the sector becomes an essential component of all foundation industries that thrive on a nation's economic growth and development.
Components of Stationary Crushing Plant
1. Jaw crusher
The jaw crusher plays the role of the first step in most instances of the overall process of crushing. The compressive force is expected to crush large-sized stones into manageable pieces. In the jaw crusher, the fixed jaw is stationary, while the moving jaw combines in a V-shaped chamber to hold the material that is fed. Because of this, it is ideal for a primary crushing stage even for the hardest stones and ores. Large input feed sizes are also supported. Because of their ruggedness and efficiency, jaw crushers hold a very important position in the mining, quarrying, and construction industry. They come in as many different sizes and capacities for meeting various operational demands; hence, they are exceptionally versatile tools in stationary crushing plants.
2. Cone Crusher
Cones crushers take the job at the secondary crushing, replacing impact crushers and hammer crushers, although impact crusher and hammer crusher can be used as secondary crushers. Cone crushers are operated based on the principle of the material being crushed between the moving steel wall and the bowl liner. In this way, the material size is reduced down until it can pass the bottom opening of the crusher. Due to the product of finely crushed material used in concrete and asphalt production, besides being used as a base material in construction projects, cone crushers are preferred. They are very useful at the stationary crushing plant because they have a wide range of crushing chambers and can take many types of stones.
3. Impact Crusher
Depending on the plant layout, impact crushers can be used for primary and secondary duty crushing. Materials are fed into a high-speed spinning rotor where it is flung against stationary plates or anvils. The resulting particles tend to be more cubic in shape, which is a major advantage when producing end products such as aggregate for flat work or structural backfill. Impact Crushers are the ones that are in high demand due to the fact that they work well to produce superior quality aggregates. They can be put to work efficiently in many applications, which have a lot of requirement regarding form, for example, road construction and production of concrete and asphalt aggregates.
4. The Vibrating Screen
Vibrating screens are quite important equipment in fixed crushing plants for separating and classifying crushed materials based on size. These are the screens that work on the basis of vibration whereby this vibration spreads the material on the surface of the screen and allows it to fall through holes of pre-defined sizes, and in this manner, it enables the feed to be separated into well-defined size fractions. In real practice, screens are requisite to make the end product consistent and qualitative. Since these are available in different sizes and types, they stand suitable to fulfill the operational requirements of crushing plants. For the fact that only material of the right size is sent to finished product stockpiles or further processing, efficient screening processes increase plant productivity.
5. Feeders
Feeder are used to control the rate at which material is fed into the crushing plant. They provide a uniform, controlled supply of material to each of the various crushers, thus preventing overloads and facilitating proper crushing. These feeders come in many types including reciprocating models, vibrating belt apron models each having a different capacity and material handling capability. Strong feeder designs greatly enhance the effectiveness and productivity of a crushing plant. They facilitate crusher performance improvement through the prevention of various problems like piling up of materials and always provide continuous smooth crushing .
6. Conveyor belt systems
The final key component to a stationary crushing plant, conveyor belts, are to move material from one stage in the process of crushing to the final product area. Without conveyor belts, the processes of crushing and screening cannot run at the same speed throughout the plant for the material to flow smoothen. The conveyors should be sturdy and of the right size, considering the volume and type of material being processed. In fact, they are key items in the optimization of plant output, since they allow the materials to move around in a fast and efficient way, minimize down times, and improve overall levels of productivity. For this reason, all these components must be adequately selected and optimized for coordination with each other in order for the stationary crushing plant to work at full capacity and profitability.
Fixed Crushing Facilities advantages
Two of the primary advantages of stationary crushing plants over mobile and compact crushing plants include a much larger volume of material they can handle and are very effective in long-term projects. Stationary crushing plants are designed to last for decades in a single location, thus making them ideal for large-scale mining or quarrying operations where the size of the deposit justifies the high setup and operating costs.
Static plants can be fitted with heavy-duty crushing equipment such as large jaw crushers and cone crushers capable of handling the initial crushing of extra-hard materials. In contrast, mobile or compact plants have been designed to run for limited time-periods, and their capacities for crushing, along with the size of the feed materials, are restricted.
Besides, stationary crushing plants offer much more options in terms of capacity customization and equipment layout for the most optimal performance, considering specific business needs. In such respect, this level of customization is considered handy in cases of working with materials that need several ways of processing or when there is a need to apply strict parameters of crushing. Stationary plants are designed with a feed of power that is for more or less constant production, using sophisticated automation and control systems, which in turn reduce labor costs, increase operational efficiency and safety, thus improving the overall throughput and quality of the crushed material. Static setups generally enable the construction of permanent infrastructure, including fixed conveyance systems, water supplies for dust suppression, and electrical connections, leading to a more stable and efficient operation.
Large stationary crushing plants form the backbone of many mining and quarrying operations around the world. Because of their unparalleled capacity efficiency, they are able to produce large volumes of material that has been precisely crushed over a longer period than mobile crushers. In addition, environmental controls can be more successfully applied in stationary plants, hence better management of emissions including noise and dust, which is becoming vital in many jurisdictions. For temporary or smaller areas, compact and mobile crushing plants possess the advantage of flexibility and mobility.
Area Used by Stationary Crushing Plants
Mining Activities
Stationary crushing plants play a vital role in the mining industry as they crush the ores or minerals extracted from a mine. These huge installations come in handy during large-scale mining since they are made to thrive under the rigors of crushing all from copper, gold, diamonds, and iron ore. The size of the raw material drawn out must be dwindled and prepared for subsequent stages of processing, such as the stage of beneficiation, which separates the valuable minerals by drawing them out. With large capacity and strong, sturdy designs, stationary crushing plants are especially apt for the hard working conditions and high demand in mining areas.
In addition, the performance of these plants can be optimized by putting together the plants in view of specific needs of given mining operations. Thus, quarries and mines can optimize the effectiveness of ore processing lines by the proper selection of crushers and auxiliary equipment so that the crushed material is of the required size and quality for further processing stages.
Quarrying
In the mining industry, stationary crushing plants are an essential part of infrastructure because of their potential capacity to optimize yields while saving energy and operating costs. That is mining. The stationary crushing plants play a vital role in quarry industries due to the ability of plants processing large stones and boulders into aggregate that is suitable for construction. These plants are designed to withstand forces from crushing hard and abrasive stones, such as granite, basalt, and limestone, to help in the building of buildings, bridges, roads, and other basic infrastructures.
A complete setup of a stationary crushing plant ensures a continuous supply of quality aggregate to the construction industry. Moreover, quarry operators can modify stationary plants according to their needs to make them more efficient and fasten the process. Equipped with integrated modern screening and washing equipment, such facilities produce aggregates that meet tight specifications in size and cleanliness for particular construction purposes, including production of concrete and asphalt. In view of the foregoing reasons, stationary plants are indispensible to a quarrying industry operation and aggregate production for building material purposes.
Aggregate Production
The businesses dealing in aggregate production rely crucially on stationary crushing plants to provide the essential raw materials required in different forms of construction and infrastructural projects. These plants perform the supply of material such as crushed stone, sand, and gravel effectively at all times by efficiently processing large volumes of raw material into good-quality aggregate. This is because stationary plants are capable of producing high-volume outputs for a wide range of aggregate sizes and types; thus, they are aptly suited to meet the varied demands of the construction industry.
Moreover, since stationary crushing plants allow for accuracy and efficiency, aggregate producers can meet particular market demand and regulatory requirements. The construction industry commonly requires aggregates of a particular gradation form and with specified durability characteristics. Because the stationary plants can produce only those aggregates which precisely meet specifications through the careful selection and configuration of crushing and screening equipment, they are essential to the supply chain necessary to undertake infrastructure and construction projects.
The mining and aggregate production industries are highly dependent on stationary crushing plants. They can provide the needed reliability and efficiency to transform raw materials into usable forms. The support they offer to major economic sectors justifies their being essential elements in global industrial processes.
MOBILE CRUSHING AND SCREENING PLANTS:
MOBILE HARD STONE CRUSHING PLANTS: The Mobile Hard is a perfect solution for crushing very hard rocks with high abrasiveness and Silica (SiO2) ratio such as granite, basalt, gabbro etc.
MOBILE JAW AND IMPACT CRUSHERS: Mobile Jaw and Impact Crushers are specific but also the most commonly produced member The Mobile Crushing Plants range.
MOBILE LIMESTONE CRUSHING PLANTS: The Mobile Limestone Plants are a special type of Mobile Crusher which are generally preferred for crushing of relatively softer stones such as limestone.
MOBILE SAND MAKING PLANTS: Our company manufactures different types and sizes of Mobile Sand Making Plants.
Components of Mobile Crushing and Screening Plants
1. Feeder
The feeder controls the flow of stones and minerals into the crushing equipment making it a crucial part of mobile crushing and screening plants. Feeders provide a constant and regulated material delivery avoiding jams and enabling a steady processing rate. They do this by using a system of conveying belts or vibrating mechanisms. In addition to increasing crushing efficiency this prevents overloading and underloading which increases the equipments lifespan. The demanding circumstances of mining and quarry operations are intended to be withstood by feeders. They have strong construction and could have pre-screening features like grizzly bars. This enhances productivity and lessens crusher wear by enabling the removal of fine material prior to it entering the primary crushing unit.
2. Grinders
The crusher is the primary device used to reduce the size of stones and minerals in any mobile crushing and screening plant. Jaw crushers impact crushers cone crushers and occasionally even hammer crushers are among the different types of crushers available contingent on the material to be processed and the intended use. Various types function differently and are selected according to the type of input stone and the required size of the output material. For example jaw crushers crush the stones using two stationary and one moving plate. However in cone crushers the material is crushed and ground by means of a rotating cone housed inside a bowl. Impact crushers smash rocks against hard surfaces by using a rotating rotor that moves quickly. The selection of crusher affects the plants capacity to handle hard abrasive materials output size and overall efficiency.
3. Belts for conveyors
The mobile crushing and screening plants main means of transportation are conveyor belts. From the feeder to the crusher and subsequently to the screening apparatus they transport the crushed stones and minerals from one step of the process to the next. Convoyers are essential to the continuous operation of the plant because they need to be strong and able to handle heavy loads of material every day. Made of materials resistant to deterioration these belts come in a variety of widths and lengths. Often spill prevention and smooth material deposit into the subsequent stage of the process are built into the design. In order to maximize throughput and minimize the chance of downtime mobile crushing and screening plants require proper conveyor maintenance.
4. Screening apparatus
For later use or further processing screening equipment divides the crushed stones and minerals into various sizes and grades. These devices separate materials according to size using a range of screening media such as wire mesh or perforated plates. The final products requirements determine the screening media to be used which can have a big impact on screening effectiveness. Typically mobile plants use vibrating screens to shake the material through various-sized sieves. This procedure is essential for guaranteeing a constant quality of product and for separating materials that require additional crushing from those that are ready for use. Mobile plants screening equipment is made to be easily assembled and disassembled enabling rapid modifications to suit a variety of project requirements.
5. The Control System
The mobile crushing and screening plants control system is its brain supervising all activities and making sure everything goes without a hitch. Modern plants are equipped with sophisticated computer-based control systems that enable real-time process monitoring. From a central control panel or even remotely operators can change parameters like the vibrating amplitude of the screens the pressure inside the crushers and the speed of the conveyor belts. These systems have safety features like emergency stop buttons and malfunction alarms to safeguard both the workers and the machinery. Complex control systems are also capable of monitoring production rates and efficiency giving useful information for improving operations. Control systems are essential to mobile crushing and screening plants because they enable prompt response to changing conditions and central troubleshooting which boosts productivity and decreases downtime.
Usage Areas of Mobile Crushing and Screening Plants
1-Extracting
Mining companies make extensive use of mobile crushing and screening plants. These systems play a crucial role in the processing of mined ores and minerals reducing their size to a manageable level so that they can be used directly or processed further. It is possible to crush and screen materials directly at the extraction site because of their mobility which makes it simple to move them to different mining locations. This lessens the need to ship heavy loads of raw materials over long distances which lowers the environmental impact and saves money on transportation. Furthermore whether for large-scale mining projects or smaller-scale operations the scalability of mobile crushing and screening plants allows them to be modified to meet the output requirements of particular mining operations. Because of their sturdy construction they can effectively process a variety of materials from softer minerals to hard rock (stone) even in the harsh conditions frequently encountered in mining environments.
2. Development
Construction aggregate is a basic material used in building and road construction and mobile crushing and screening plants are essential to the production of different grades of this material in the industry. These plants give contractors the freedom to crush and screen stone right at the construction site giving them the precise amount and quality of material required for a given project. Building projects can have a much smaller carbon footprint and pay much less for material transportation thanks to this on-site processing capability. Mobile plants can also help recycle waste from construction and demolition turning it into valuable aggregate that can be used again in future projects. By lowering the need for new materials sourced from quarries this not only aids in waste management but also supports sustainability initiatives in the construction sector.
3. Quarries
Portable crushing and screening equipment is very advantageous for quarry operations. For quarried stone to be processed effectively and become high-quality aggregate for use in a variety of applications such as the creation of concrete asphalt and materials for road bases these plants are necessary. One benefit of mobile plants is their ease of mobility and quick setup which lowers downtime and boosts output. Quarry operators can satisfy a wide range of market demands thanks to their flexibility in handling various stone types and sizes. Mobile plants are vital assets in quarrying operations because they integrate cutting-edge screening technology to guarantee that the finished product satisfies stringent size and quality specifications.
4. Reusing
To process a range of recyclable materials such as concrete asphalt and glass the recycling industry has been using mobile crushing and screening plants more and more. Because they reduce landfill waste and the consumption of natural resources these plants play a crucial role in turning these materials into usable aggregate and promoting sustainability. Utilizing mobile plants materials can be processed on-site and prepared for reuse in new construction projects. These plants can be swiftly deployed to recycling sites. This is a financially sensible way to manage waste from construction and demolition while also promoting environmental sustainability initiatives. Due to their ability to handle a wide variety of materials mobile crushing and screening plants are becoming an indispensable component of contemporary recycling operations and supporting the circular economy.
Working Principle of Mobile Crushing and Screening Equipment
In order to reduce big chunks of stone and other materials into smaller more manageable sizes for a range of applications mobile crushing and screening plants work by coordinating a series of coordinated actions. First materials like stones are fed into the feeder which controls the flow of materials to the crusher so that the stream is steady and easy to handle. Afterwards the stone is reduced in size by the crusher this may involve a jaw crusher for initial crushing followed by cone or impact crushers for additional size reduction depending on the particular configuration. Following crushing the material is sent to the screening stage where vibrating screens or other screening technologies are used to separate it into various size grades. Mobility and adaptability are the true assets of mobile crushing and screening plants. Their ability to be swiftly relocated and configured to commence processing instantaneously sets them apart from stationary plants rendering them perfect for transitory projects or scenarios requiring the operation to be shifted around a quarry mine or construction site. Effective operation is ensured by their integrated control systems which facilitate prompt adjustments to production demands. Because of these attributes mobile crushing and screening plants can operate in a range of environments and applications with great productivity and adaptability to meet a variety of material processing needs.


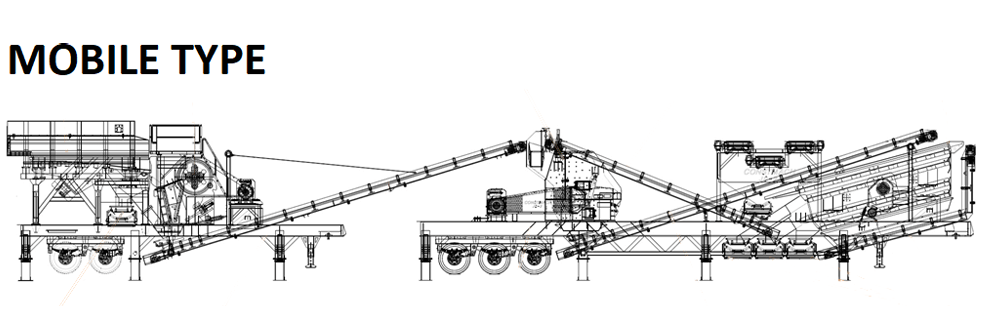

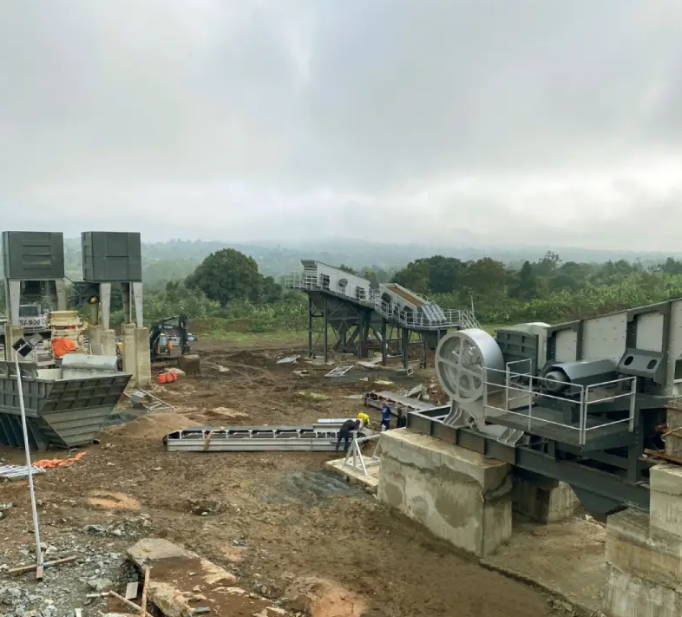


