Prestressed Carrousel Concrete Sleeper Manufacturing Plant
CARROUSEL SYSTEM SLEEPER PRODUCTION METHOD
The invention relates to a method of manufacturing a concrete sleeper comprising the following steps: insertion of pre-stressing rods into a sleeper mould, tensioning of the pre-stressing rods, filling of the sleeper mould with concrete, leaving the concrete to harden and removal of the concrete sleeper from the mould.
For the manufacture of pre-stressed concrete sleepers, sleeper moulds are used which are continuously in rotation. After cleaning of the sleeper moulds, they are filled with liquid concrete, then they pass through a shaking station. The hardening time of the liquid concrete poured into the sleeper moulds can be shortened by applying heat,
e.g. in a heat chamber. If the concrete has sufficient hardness, the sleeper moulds are lifted and turned over so that the concrete sleepers can be removed from the mould.
Conventional concrete sleepers usually have four embedded pre- stressing rods, which are disposed in two rows, spaced apart laterally. Sleepers with a reinforcement of this type are however only suitable subject to certain conditions, if at all, for high axial loads.
These conventional pre-stressed concrete sleepers are manufactured in the rotation method. In this, all four pre-stressing rods are tensioned simultaneously and automatically, but individually and are de-tensioned in exactly the same way.
Sleepers are also known having eight pre-stressing rods, which are tensioned simultaneously and automatically and de-tensioned again, and in the conventional method with more than four pre-stressing wires, these are then gathered into bundles composed of at least two pre-stressing rods each and then these bundles are tensioned together.
The object of the invention is to indicate a simple, economical method of manufacturing a concrete sleeper which is suitable for high axial loads.
In the method according to the invention, it is preferred that both ends of a pre-stressing rod have a thread and one end is anchored in a tie bolt spindle and the other end is tensioned with a tensioning spindle and fixed with spindle nuts which bear on the sleeper mould. In order to tension, a pull is exerted on the tensioning spindles and then the nuts are screwed on to the thread, retaining the necessary bias in the pre-stressing rod.
It is particularly preferred that pre-stressing rods are used having a ribbed or profiled surface. With such a surface, a firm adhesion is created between the pre-stressing rod and the surrounding concrete and hence good transmission of force.
Within the scope of the invention, it can be provided that plural, preferably two to four, adjacent concrete sleepers are manufactured in one sleeper mould. Thus a larger number of concrete sleepers can be manufactured simultaneously. Further method features are described in the subclaims.
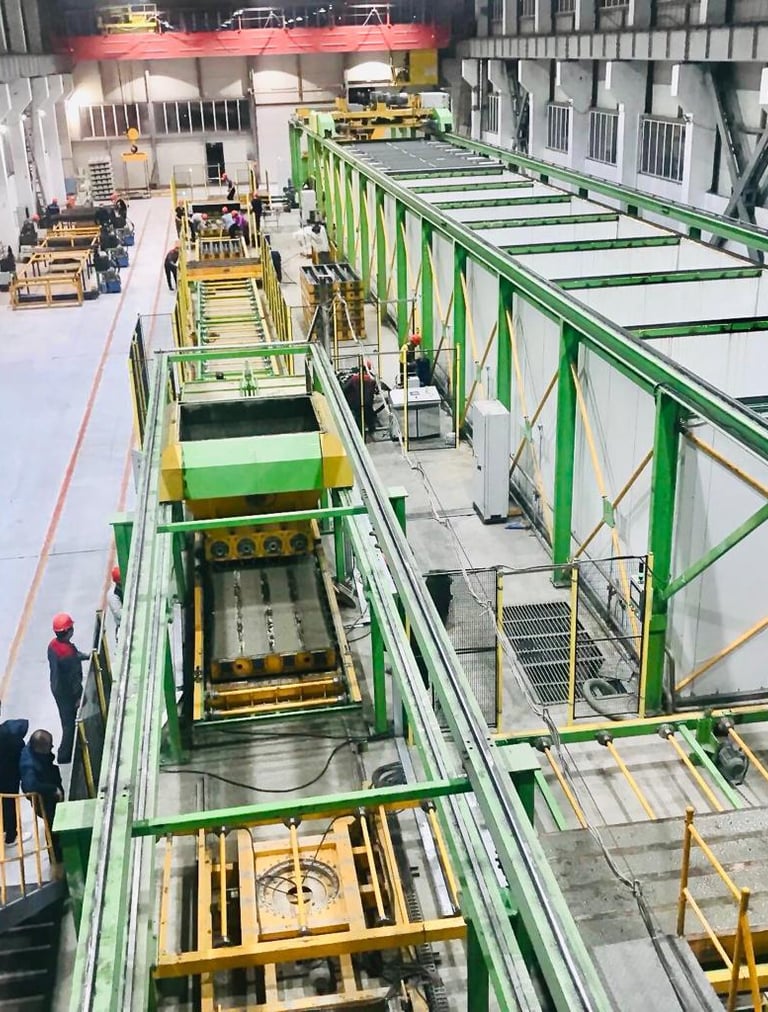
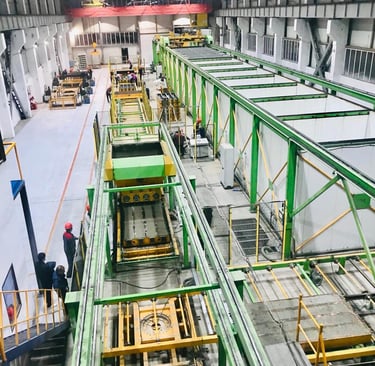
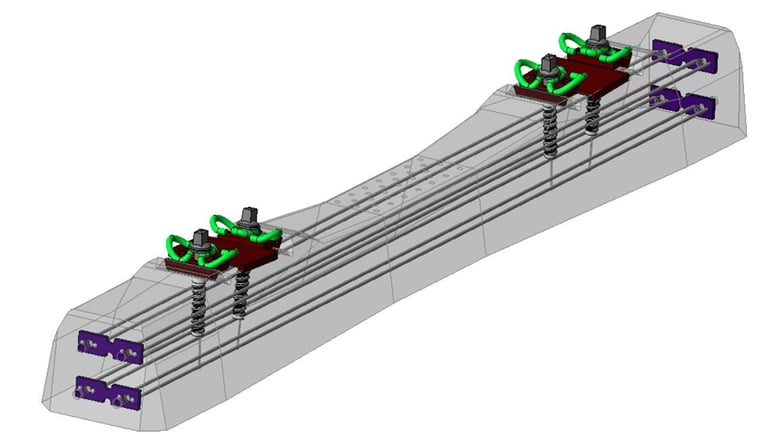
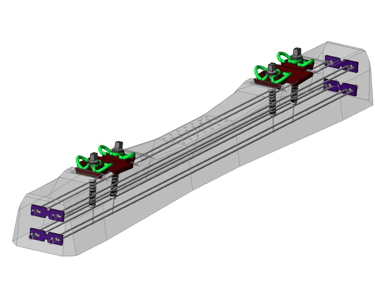
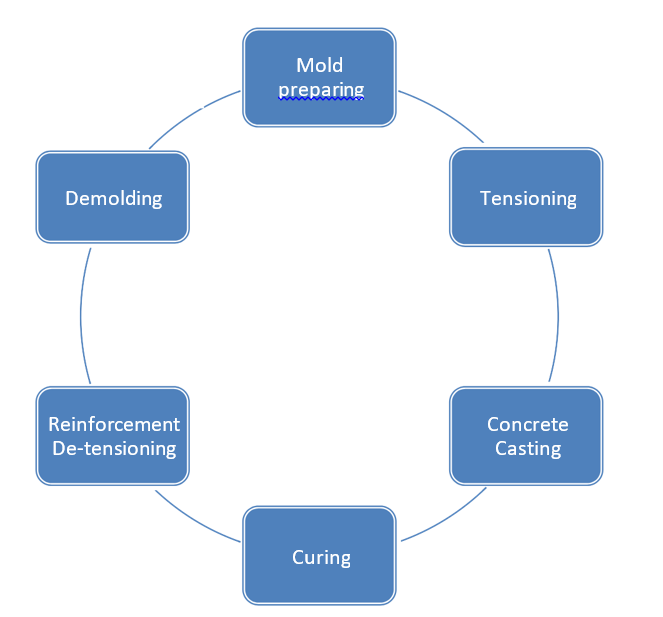
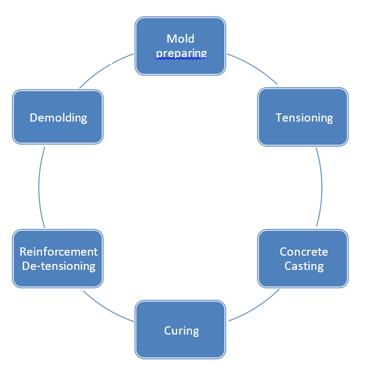
· Sleeper Mould
Many different sleeper types are used in the world. Concrete sleeper types have different designs due to their intended use and regional standards of countries.(EN,GOST,AREMA-B70,B07,B320)
First of all, pre-stressed concrete sleeper molds are designed in solid programs according to the sleeper design given by the customer.
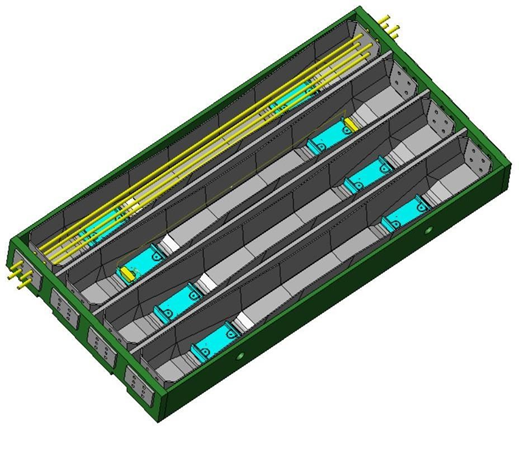
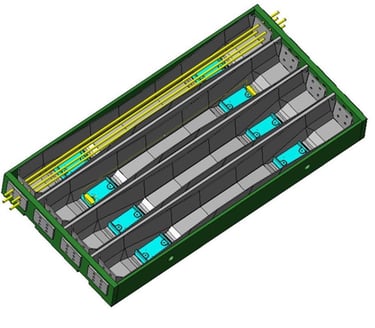
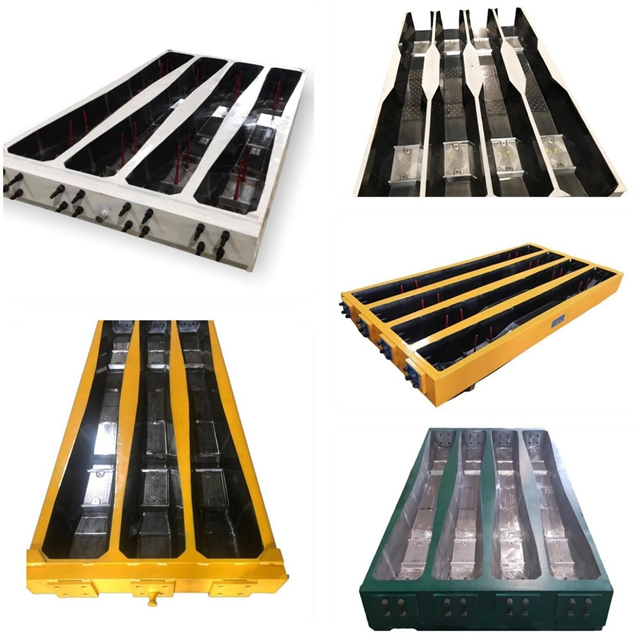
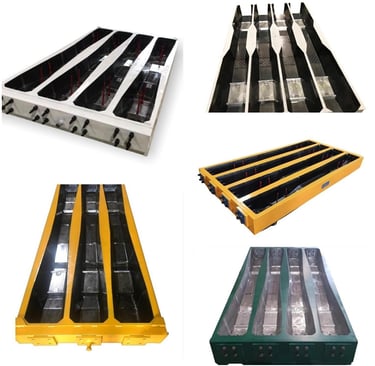
SLEEPER PRODUCTION MACHINES & SYSTEMS
· Mould Transfer Conveyor System
The conveyor system is used to automatically or semi-automatically transfer the concrete sleeper molds to the next station.
Three different types of conveyors are used in the system.
1. Roller Conveyors.
The drive unit for the roller conveyor consists of one drive sprocket and two deflect sprockets. The drive sprocket
is driven by an electro motor, located on the inside of the drive unit.
The transportation rollers are driven by a chain running on the side of the drive unit.
Technical data:
Electrical power rating 2,2kW
Drive speed (infinitely variable) 0 - 0.4 m/s
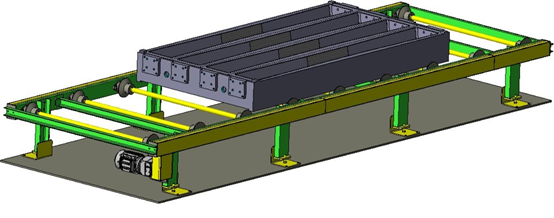
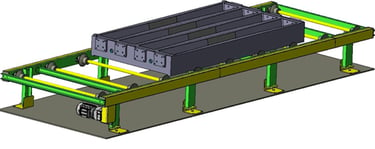
2. Rotary Roller Conveyors (90 degree)
These rotary conveyors return to the duty station automatically or semi-automatically when the concrete sleeper molds find their position on the conveyor, and return to the next station after the process is finished.
Technical data:
Electrical power rating 2,2 kW
Drive speed (infinitely variable) 0 - 0.4 m/s
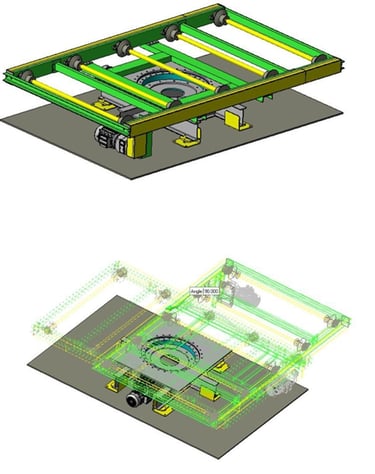
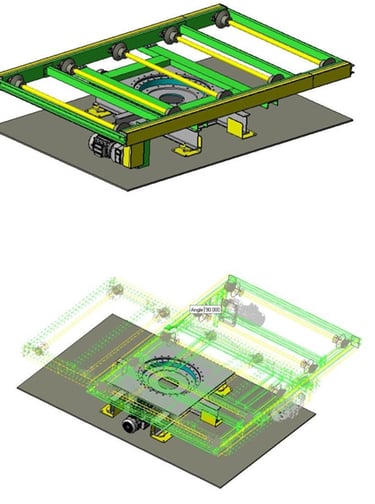
3. Moveable and Rotary Conveyor
These conveyors automatically take the concreted sleeper molds and distribute them to the double conveyor belonging to the automatic mold transfer robot.
Technical data:
Electrical power rating 2,2 kW
Drive speed (infinitely variable) 0 - 0.4 m/s
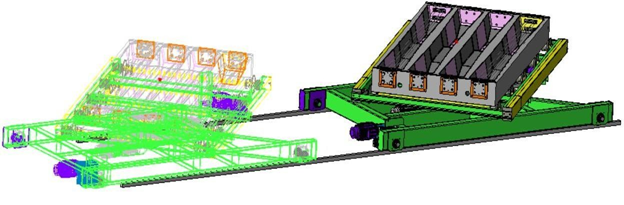
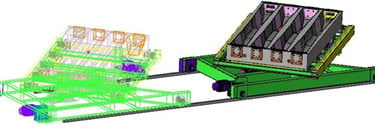
4.Hydraulic Lifting &Moveable Conveyors
These conveyors are used to move the sleeper molds coming out of the curing chambers to the Relaxing station step by step. The system works with the principle of moving the molds or traverses back and forth by lifting them with hydraulic pistons.
Technical data:
Electrical power rating kW
Drive speed (infinitely variable) 0 - 0.4 m/s
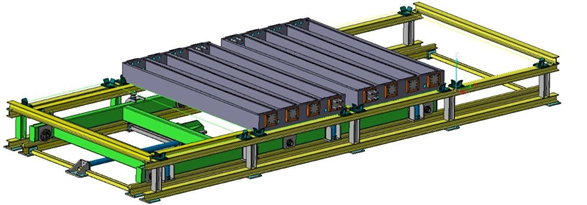
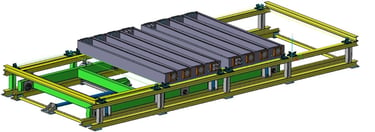
Hydraulic Mould Transfer Conveyor
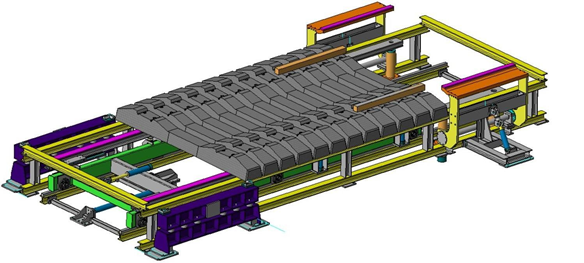
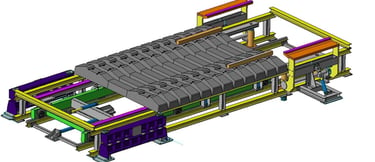
Hydraulic Sleeper Transfer Conveyor
Tensioning Machine & Station
The reinforcement cages are tensioned by the tensioning machine through the tie rods at the required force. The machine is provided with 1 tensioning head with 4 tensioning cylinders and the tensioning is provided simultaneously for each tie roads and for one cavity at a time. Tensioning force can be change with governments and standards.(EN,AREMA,GOST)
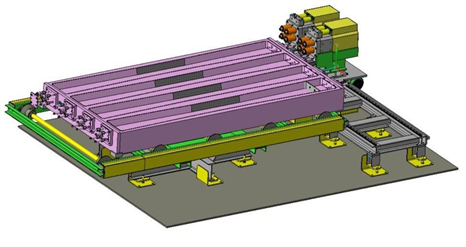
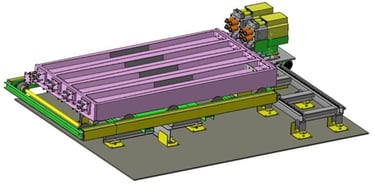
Technical Data:
QUADRUPLE SCREW JACK, 460KN
- Stressing force max. 460 kN at 370 bar
- Stressing stroke 80 mm
- Spring-supported wrench head, 30 mm AF
- Support M20-WAF30
STATIONARY HYDRAULIC PUMP UNIT
Basic unit for double/triple/quadruple/sextuple screw jacks
- HIGH-PRESSURE PUMP 8.4 L/MIN
for 5.5 kW motor for triple and quadruple screw jacks
- STAGE ELECTR. EQUIPMENT PLC
- For 8.4 lt/min pump
- Pump motor: 5.5 kW, 400 V, 50/60 Hz, 1500 rpm
- Spindle drive: 0.6/2.0 kW
- PLC controlled, for triple/quadruple screw jacks
400 V/50 Hz, for double, triple and quadruple screw jacks
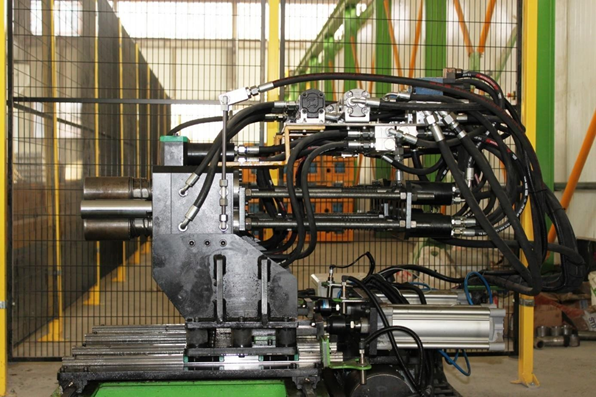
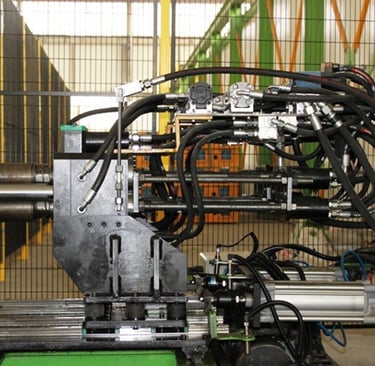
Technical Data :
Travel distance longitudinal : 50.500 mm
Travel distance transversal: 4.000 mm
Lifting height: 4.000 mm
Mould Length: ? mm
Mould Width: 1.500 mm
Sleeper per Mould: 4 pcs.
Lifting Capacity: 6.000kg
Gauge manipulator approx.: 4.300 mm
Wheels: 4 pcs.
Horizontal guiding: 4 pcs.
Wheel diameter: 400 mm
Positioning accuracy: +/- 1.5 mm
Deceleration: 0,7 m/s
Lifting traverse: 2 pcs.
Travel speed longitudinal: 0 – 1,0 m/s
Travel speed transversal: 0 – 0,3 m/s
Lifting speed when loaded: 0 – 0,5 m/s
Lifting speed when unloaded: 0 – 0,5 m/s
Lifting Power: 30 kW
Power Drive Motor: 2 x 5,5 kW
Power Gripper Unit: 0,75 kW

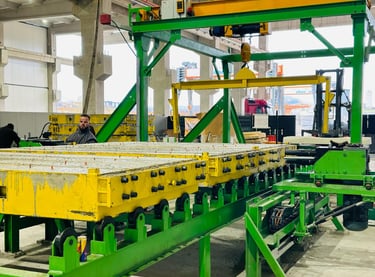
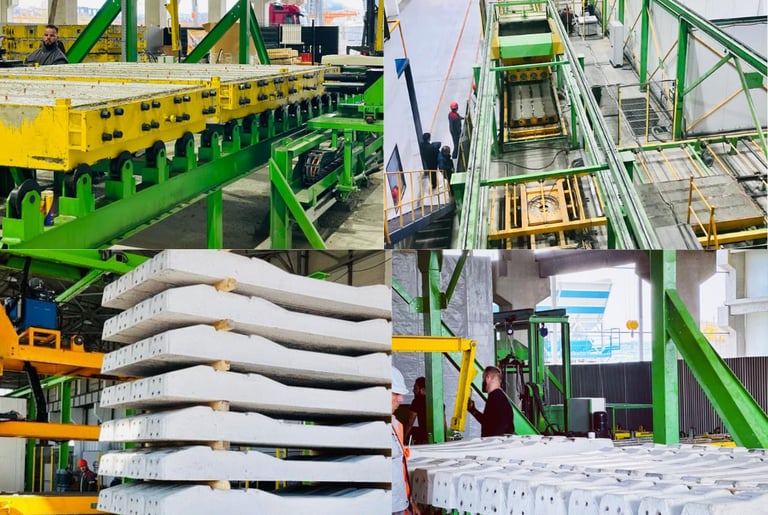
